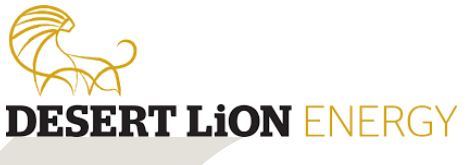
The Desert Lion Energy Lithium Project is located in the mining-friendly jurisdiction of Erongo, Namibia. The project is situated on open semi-arid, scarcely populated lands, approximately 120 km to the north-west of Windhoek, the capital city of Namibia. The site is 30 km south-east of Karabib, providing proximity to excellent infrastructure. This mine was first discovered in the 1930s and has a long history of small-scale mining operations. Massive volumes of dumps from the historic mining are located around the Rubicon 1 and Rubicon 2 open pits. These dumps contain material from the historic open pit and underground mining, and consist of a mixture of ore, waste and tailings resulting in very heterogeneous dumps.
This posed a challenge to the potential processing of the dumps because the processing facility would require a
consistent flow of ore at a very consistent grade.

We managed to feed a consistent grade to the processing plant by developing a practically executable mine plan blending material from 19 Dumps
between the 19 dumps. Utilising the material-blending capabilities of GEOVIA MineShed™ software, Minxcon set up a material flow network detailing the requirements to achieve the blending strategy.
Minxcon was able to practically mine and efficiently blend the material from the 19 dumps feeding the plant a
consistent grade by following the resulting loading ratio.